Four factors to improve production efficiency
1. Accuracy of standard operating time
The assembly line operation manual is not only the operation guide but also includes the standard of the operation time, the matching of materials, and so on and sends the comprehensive technical data to the production process personnel.
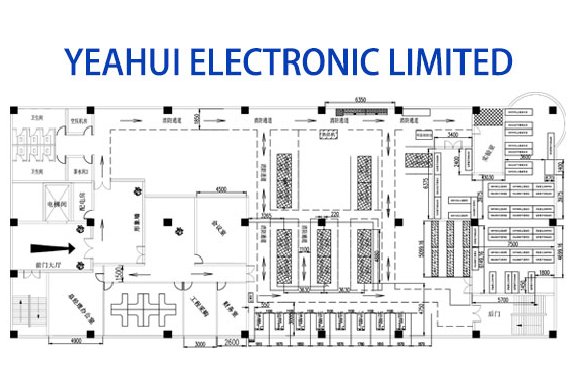
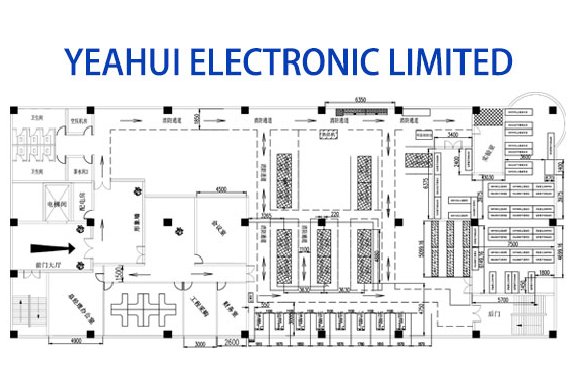
Why mention operation time? Production efficiency refers to the ratio between the actual output of the process and the maximum output under a fixed input. It can reflect the degree of achieving the maximum output, the predetermined goal, or the best operating service. It can also measure the performance of economic individuals under output, cost, income, or profit. Therefore, the wire harness industry is no exception, and this standard operating time has a greater impact on the field of wire harness processing and production efficiency, because at present, whether it is a domestic company or a foreign company, such as a German wire harness factory, a factory that has been ranked globally, the proportion of manual operations is still very large of.
Second, the rationality of the site layout
There are several premises that should be considered for the layout of the workshop, which must be ensured: the clarity of lighting, the safety of access and operation, and the zero contact between the staff aisle and the equipment; and the convenience of maintenance and other site requirements of 5s or 6S.
In addition to ensuring these basic requirements, rationally optimizing the layout of on-site workshops is also an important strategy to improve production efficiency.
1. Reasonably arrange the work area according to the nature of production
For example, wire harness production is divided into automatic thread cutting, automatic crimping terminals, small rubber plugs, etc., and then auxiliary operations such as the manual operation of all large terminals and heat-shrinkable tubes. Similar to this kind of undertaking relationship, there is a necessary sequence of operations, and it should be reduced to the connection distance on the way. Ensure the smoothness of production.
2. According to the actual production materials, avoid the cross circuit of material movement
Conditional and feasible materials, such as small rubber plugs, protective hoses, and other materials can be used as spare materials in each area of use. Like some large materials or semi-finished products that take up space, they should be placed in the appropriate area of the operator as much as possible, saving the time cost of taking materials back and forth.
Three, technical depth, man-machine combination
Although many operations are currently mechanized, such as automatic wire cutting, de-insulation, crimping terminals, and even more advanced equipment that can automatically insert terminals into the jacket, this equipment is very expensive. However, whether it is operating equipment or manual processing is carried out by someone, so it is very important to deepen the training of employees.
1. Reasonably arrange employee advantages
Women can be arranged in the automatic processing area, and the materials can be distinguished more carefully; men can be arranged in the manual area, such as crimping of the terminal, to give full play to the advantages of physical fitness.
2. According to the technological requirements, combined with the feasibility of man-machine
On the premise of meeting the technical requirements, the human-machine functions should be guaranteed as much as possible, such as the convenience of letting workers raise their hands and turn around and other basic actions.
3. Strengthen training for employees
Fourth, optimize production methods
The characteristics of wire harness products, especially vehicle wire harnesses are more prominent. On a pipeline, different units of wire harnesses will be jointly processed into a fully functional wire harness product. Therefore, the processing method and processing in different areas are the overall cost of time. There is a big difference.
There is no basic principle for optimization that can be carried out, and the only optimization is based on the actual conditions of specific workshops and specific pipelines.
Because the optimization content is not fixed, here is a brief explanation about the specific process of optimization:
After production finds problems-process analysis problems, summarizes the problems-organizes production meetings to discuss the problems and determine whether they can be performed, such as whether welding of the wiring harness is done in the final assembly or processed before pre-assembly. Go to the assembly line for further processing-and then organize the project to discuss the technical feasibility and so on.
Summary: Production efficiency means using fewer people to produce a larger qualified product output within a certain equivalent time.
Yeahui is a connector supplier with 11 years of experience in developing high-quality connectors and wiring harnesses. We have many types of products, including obd connector, circular connector, agricultural connector and so on. We can meet the requirements of various customers. Feel free to learn more about connectors or buy our connectors, looking forward to your message.
More about COVID-19(Work to improve the efficiency of harness processing).
评论
发表评论