Common mistakes in assembling cables
The assembly process of the cable must be carried out with great care, as any defects in the production assembly process can cause an overall failure of the product, resulting in an accident. Although manufacturers are aware of the seriousness, they still make some common mistakes when producing assembled cables. Below is a list of six common mistakes that cable manufacturers have in the assembly process of electronic cables.
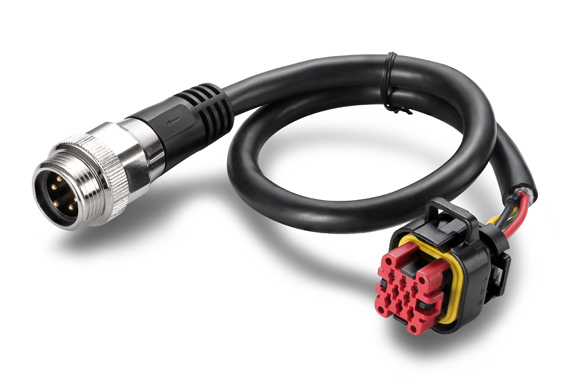
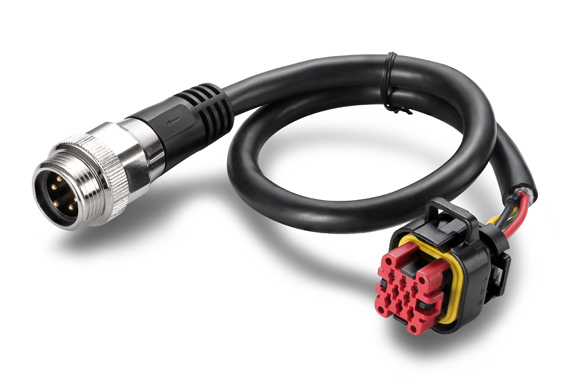
Prepare the wire
Preparing the wires must be performed with care and precision, as it determines the overall efficiency and performance of the components. Many manufacturers have made mistakes in this first phase, chose the wrong wires, and finally need to cut the plug and then use the plug to connect the correct wires.
Do not follow the assembly drawing
Failure to follow the assembly drawing can cause problems in connecting the wires in the chassis. Cable manufacturers often incorrectly connect the wires, which can cause the wire assembly to fail, resulting in failure of the entire system. The assembly drawing must be strictly followed to avoid such error.
Defects in crimping
The crimping process involves terminating the cable in the cable, which is the most critical step in the cable assembly and can result in an open or short circuit if not properly performed. If the manufacturer does this at will, it is easy to cause product failure.
Incorrect welding
Incorrect soldering is another manufacturing process that many manufacturers make mistakes,which can cause thermal damage. When doing this, use the correct soldering equipment and the correct soldering temperature.
Missing wires and using the wrong hardware
To meet project schedules, some cable manufacturers may tend to ignore wires that are critical in assembly. This can lead to failure of the cable assembly and, in addition, the manufacturer may use the wrong hardware, including brackets, clamps, washers or screws to assemble the cable.
Incorrect wire connection
The final step in the cable assembly process is to bundle the wires with plastic straps. Sometimes the cable manufacturer tightens the package too much to damage the wires. On the other hand, if it is loose, it may not be able to hold the bundle correctly, so the manufacturer must ensure that the tie is fastened around the wire in the correct manner.
Yeahui is a connector supplier with 11 years of experience in developing high quality connectors and wiring harnesses. wo have many types of products, including obd connectors, circular connectors, agricultural connectors and so on.We can meet the requirements of various customers. Feel free to learn more about connectors or buy our connectors,looking forward to your message.
Read more about the connectors(Standard design of electronic cables).
评论
发表评论